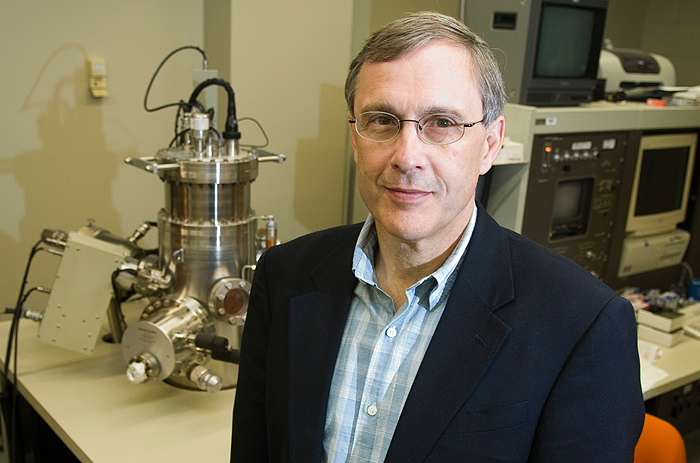
Carbon capture has long been identified as a critical technology needed to prevent global warming, but efficient and economical ways to do it have been hard to find.
A new process to capture and convert carbon dioxide, discovered by a UConn chemist in the College of Liberal Arts and Sciences, has just been awarded a patent. It uses cheap catalysts, electricity, and heat to convert CO2 and water into useful chemicals or fuels.
Steve Suib, Board of Trustees Distinguished Professor of Chemistry and the 2011 Connecticut Medal of Science winner, found a way to use metal oxides, such as manganese and zinc oxides, as catalysts in a conversion process that also uses heat and electricity.
The newly patented method can be run as a continuous, rather than a batch, process, to yield large amounts of a product. What is made depends on the catalyst used. Potential products include paraformaldehyde, used in disinfectants and in chemical processes in industry, or ethylene, the largest bulk chemical in the world, used in products such as milk bottles.
The process could also be used to generate hydrogen and a variety of hydrocarbons.
“You can make a significant amount of material at high conversions over a long period of time,” Suib says.
CO2 and H2O are abundant but hard to activate in a chemical process, Suib points out: “It is difficult because both of those molecules are relatively stable.”
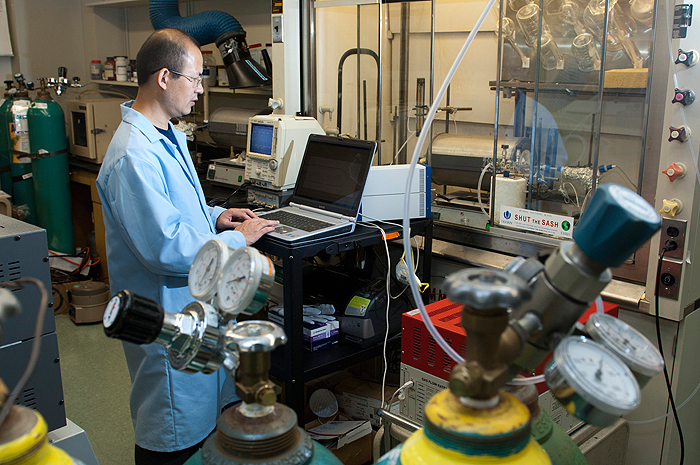
The process was developed in Suib’s lab, and Ph.D. candidate Boxun Hu, soon to graduate, was heavily involved in the work, which will be published, Suib says.
The patent was granted in late June. It improves on an earlier process that Suib patented in 2009, which used a more expensive catalyst—platinum—and produced little product. The earlier process was the subject of a 2010 paper in the journal Applied Catalysis Part A.
Both patents are jointly held by UConn, through the Office of Technology Commercialization, and Catelectric Advanced Electrocatalysis, a company that began as part of UConn’s Technology Incubation Program. Catelectric specializes in improved catalysis processes.
Suib has received research grants from Catelectric to work on the process. He has also had extensive Department of Energy grant funding, and is the lead researcher on a $1.8 million DoE grant to make catalysts for a pilot biomass conversion plant that will be built at UConn.
Suib’s latest patent—he has about 50—is a combined process and composition of matter patent. While process patents can be hard to enforce, Suib says—it is difficult to tell whether a possible infringer is varying or using the same process—the composition of matter component of the patent makes infringement easier to pinpoint.
If the newly patented process is used, UConn would get royalties from the use.
The next step would be to take what is a rather crude, laboratory process and scale it up to the pilot plant stage for testing, and eventually to the manufacturing stage, Suib says.
The costs of heat and electricity used in the process would then be considerations. Electricity costs are high in Connecticut compared with other states, Suib notes. The technology of capturing heat, and even excess CO2, from existing manufacturing plants might be considered, allowing factories to use their excess heat in a process that would result in making new chemicals.
The “Buck Rogers” idea now being floated is to capture heat escaping from nuclear power plants and use that as a heat source, he says.
The effort to capture and convert CO2 into useful products, mitigating global warming in the process, is one that has captured his interest: “A lot of people say, ‘you just can’t do this’—but those are the problems that are interesting.”
Suib will be made a fellow of the American Chemical Society at its August meeting in Denver. He was previously designated a “Chemical Pioneer” by the American Institute of Chemists.