[yframe url=’http://www.youtube.com/watch?v=mXF3aWWfRKI&feature=youtu.be’]
The University of Connecticut and Pratt & Whitney today celebrated the opening of a new Pratt & Whitney Additive Manufacturing Innovation Center at UConn, one of the most advanced additive manufacturing laboratories in the nation.
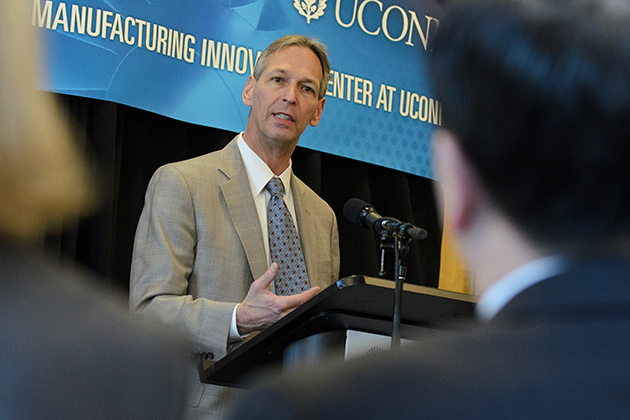
The Pratt & Whitney Additive Manufacturing Innovation Center, a collaboration between UConn and Pratt & Whitney, will be used to further additive manufacturing research and development and is the first additive manufacturing facility in the Northeast to work with metals rather than plastics. The center also will be used to train a new generation of engineers and designers in the latest advancements in manufacturing technology.
“The University of Connecticut’s outstanding technical capacity complements our fundamental research needs and will help us continue to grow our additive manufacturing capabilities,” said Paul Adams, Pratt & Whitney’s chief operating officer. “Additive manufacturing is complementary to traditional methods by enabling new innovation in design, speed and affordability, and is necessary to build the next generation of jet engines. We are currently using additive manufacturing to build complex components with extreme precision for the flight-proven PurePower commercial jet engine.”
The University of Connecticut’s outstanding technical capacity complements our fundamental research needs and will help us continue to grow our additive manufacturing capabilities.
Located on UConn’s Depot Campus in Storrs, the Pratt & Whitney Additive Manufacturing Innovation Center features the latest in 3-D manufacturing equipment and rapid prototyping technologies. It is home to two Arcam electron beam melting (EBM) A2X model machines for the manufacturing of large, complex metal parts at high temperatures. The A2X models are the first to be introduced in North America and the two EBM machines are believed to be the first of their kind in the Northeast. The UConn center recently provided the first EBM on-site training for academic personnel and industry engineers in the United States.
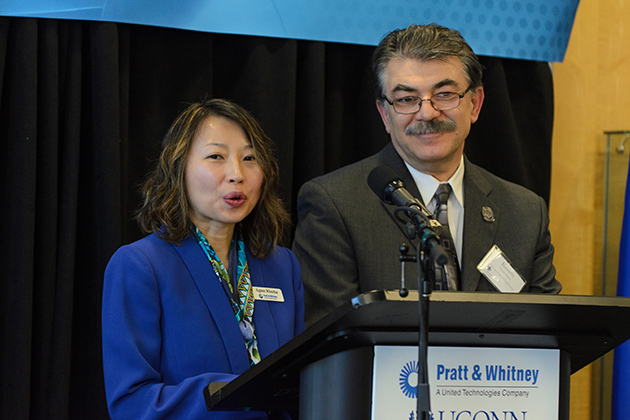
Pratt & Whitney engineers and UConn faculty and students will use the center’s resources to develop advanced fabrication techniques for complex production parts that are in high demand in aerospace, biomedical science, and other industries. Over time, the Pratt & Whitney Additive Manufacturing Innovation Center at UConn is expected to elevate Connecticut industries’ production capabilities, reduce manufacturing times, eliminate material waste, and allow for the creation of a new generation of intricate, light-weight, and durable custom products.
“This unique partnership between Pratt & Whitney and UConn is an excellent example of the innovation and collaboration that will drive Connecticut’s future economic success,” said UConn President Susan Herbst. “The new Pratt & Whitney Additive Manufacturing Innovation Center will allow us to push into new frontiers of manufacturing and materials science while training a new generation of engineers in some of the world’s most sophisticated manufacturing technology.”
Pratt & Whitney, a United Technologies Corp. company, invested more than $4.5 million in the Pratt & Whitney Additive Manufacturing Center and over the next five years will invest an additional $3.5 million in the facility. In 2010, Pratt & Whitney established a research Center of Excellence at the University of Connecticut. The Pratt & Whitney Center of Excellence at UConn focuses on fundamental and applied research initiatives that support the design and development of more efficient gas turbine engines. UConn’s primary research is in the field of advanced sensors, diagnostics, and controls.
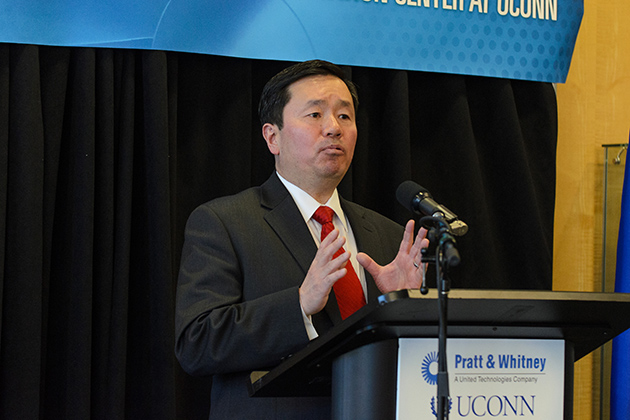
The new Pratt & Whitney Additive Manufacturing Innovation Center supports President Obama’s Advanced Manufacturing Partnership initiative. This initiative, launched in 2011, encourages innovative collaborations between industry, universities, and the federal government in order to increase the nation’s global competitiveness by improving existing manufacturing capabilities through the development of advanced materials, components, and technologies.
As a teaching and research center, the new facility will assume a pivotal place in UConn’s new Technology Park scheduled to open in 2015 in Storrs. The University of Connecticut is developing new degree concentrations and a new curriculum associated with additive manufacturing. The additive manufacturing innovation center also will host workshops and training sessions for students and engineers interested in the latest technology. Other Connecticut manufacturers will be invited to explore additive manufacturing for their own product design and development.
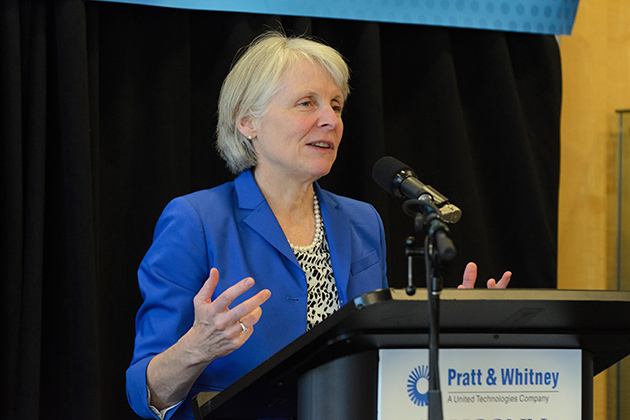
“Under Governor Malloy, economic development strategy is based upon building a strong relationship between the state, the private sector, and our institutions of higher learning. The Additive Manufacturing Innovation Center is the latest example of the structural and strategic changes we’re making,” said Catherine Smith, Commissioner of the Connecticut Department of Economic and Community Development. “From Bioscience Connecticut and Jackson Labs; to workforce development through our manufacturing technology programs at our community colleges; to the re-launch of the Small Business Development Center; these important investments in our state’s future are reigniting and reinvigorating Connecticut’s economy.”
Additive manufacturing is transforming industry today by allowing for innovations in design, speed, and affordability. It is complementary to traditional manufacturing, which is a “subtractive” process in which parts are made when raw metal is ground down into a shape engineers need. This process generates a large amount of material waste and often requires the assembly of multiple dependent parts to produce a single component.
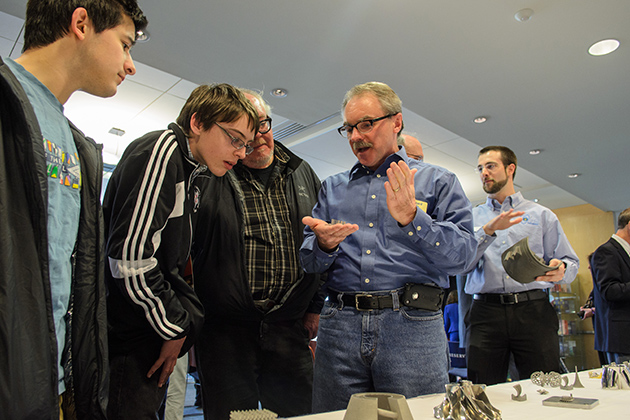
The Pratt & Whitney Additive Manufacturing Innovation Center at UConn uses advanced powder bed manufacturing technologies and high-powered electron beams and lasers to repeatedly melt fine layers of powdered metals like titanium into one solid integrated piece. This layer-by-layer “additive” process allows for the creation of extremely complex three-dimensional objects without the constraints of the traditional manufacturing process. Additive manufacturing dramatically reduces production time from design to prototyping to finished product and results in components with material properties better than cast. It also reduces the amount of raw material used and the need for tooling as parts can be made on-demand and on-site. Additive manufacturing has near limitless potential applications and can be used for a wide range of products – from advanced turbine components for jet engines to personalized prosthetic implants for patients who need them.