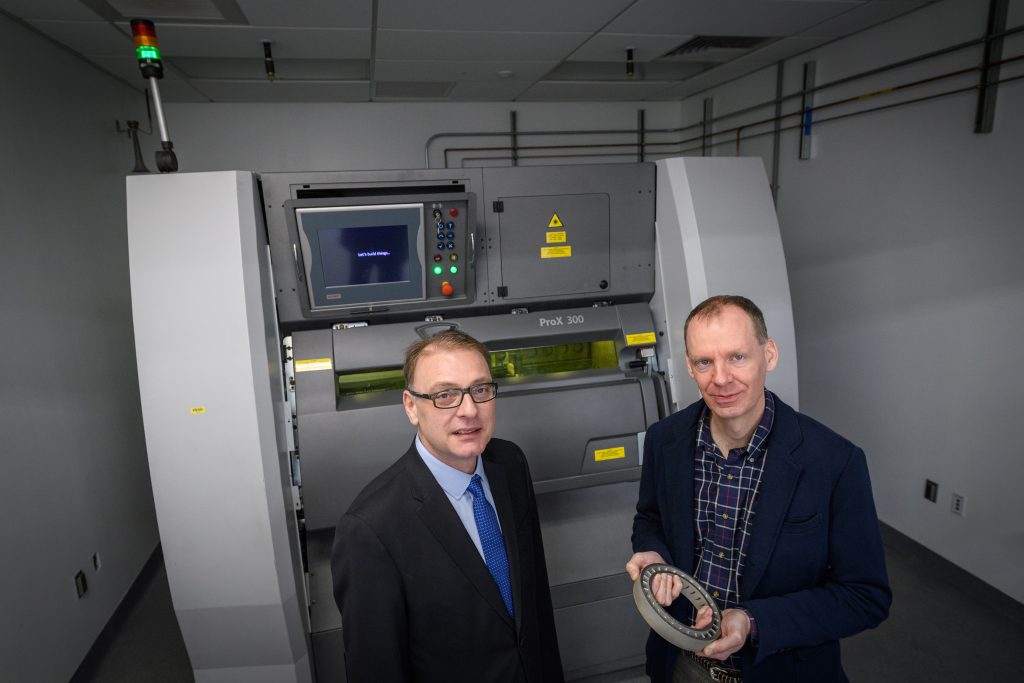
When a ship runs into trouble at sea, it can be time-consuming and disruptive to take it ashore to get it fixed. A team of UConn engineers has now developed a way for a ship’s crew to pinpoint the exact location of any mechanical trouble on board and, instead of taking the ship offline for maintenance, to repair or replace the part while the ship is still at sea.
The researchers, led by associate professor of materials science and engineering Rainer Hebert, have created a device that uses ceramics on additively manufactured metals to obtain signals about degradation or certain other potential problems, such as overheating. They are also developing a field-deployable manufacturing process that could produce replacement parts from electronic files using a 3-D printer on board ship after the metal-ceramic parts indicate failure or problems.
The new device can simultaneously carry the weight and resist temperature variants of existing components. (A change in temperature can signal a potential problem.) It then generates an electrical signal that alerts crew members, in real time, to the change in temperature and the amount of strain placed on that part.
“Essentially, what we’re trying to do is combine two completely separate materials – ceramics and metals – in an additive manufacturing environment,” says Pamir Alpay, GE Professor in Advanced Manufacturing and executive director of UConn’s Innovation Partnership Building in Storrs. “Such a combination in a 3-D printing process is unique and challenging.”
The team deposited a ceramic oxide that can sense temperature and strain variations onto an additively manufactured aerospace superalloy, Inconel. The metal is a structured, additively manufactured component that resists temperature variants. The ceramic piece generates an electrical signal that’s accessible using radio frequencies, thereby offering real-time monitoring.
“It is a proof-of-concept study that shows it is possible to do this while maintaining functional properties of the oxide,” Alpay says.
This demonstration of feasibility, published last year in Acta Materialia, is new and important, says Hebert, the director of UConn’s Pratt & Whitney Additive Manufacturing Center, because conventionally, the metals used in conjunction with ceramics on the surface possess specific characteristics that deviate from those found in additively manufactured metals of the same chemistry.
The combined metal-ceramic idea grew out of the U.S. Navy’s desire to extend its maintenance cycles. Navy staff said that if they were able to monitor critical components in real time, they would not have to take a ship offline for inspections and repairs. And if replacement parts could be manufactured on ships, the maintenance cycles might be extended even further.
Another benefit to real-time monitoring is that a localized point of stress, such as a small crack, can be detected and repaired before it turns into a major problem. Technology already exists to alert the crew to temperature fluctuations and trouble in a given zone of the ship, but signaling the exact location of the problem is new, Alpay says.
Once the replacement parts have been printed, additional processing steps will be necessary – for example heating of the as-fabricated parts in furnaces to impart specific properties, or the smoothing of surfaces. But the potential of on-demand, on-site manufacturing and self-diagnostics of structural parts certainly promises weight and fuel reductions with limited maintenance, Hebert says.
Hebert developed a 10-day training course on additive manufacturing for two engineers from the Navy’s Naval Air Systems Command (NAVAIR). The training is intended to provide hands-on experience and theoretical background information to spread knowledge of additive manufacturing and its current challenges, opportunities, and limitations more widely in the Navy.
The potential of additive manufacturing for Naval and, more widely, for defense applications is real, Hebert says, although further basic and applied research is necessary to achieve reproducible results and resilience in field use.
The Navy is not the only expected beneficiary of this discovery. This ceramic-metals combination could be useful to automotive and aerospace applications as well.