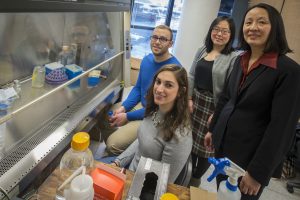
UConn researchers have created a biodegradable composite made of silk fibers that can be used to repair broken load-bearing bones without the complications sometimes presented by other materials.
Repairing major load-bearing bones such as those in the leg can be a long and uncomfortable process.
To facilitate repair, doctors may install a metal plate to support the bone as it fuses and heals. Yet that can be problematic. Some metals leach ions into surrounding tissue, causing inflammation and irritation. Metals are also very stiff. If a metal plate bears too much load in the leg, the new bone may grow back weaker and be vulnerable to fracture.
Seeking a solution to the problem, UConn professor Mei Wei, a materials scientist and biomedical engineer, turned to spiders and moths for inspiration. In particular, Wei focused on silk fibroin, a protein found in the silk fibers spun by spiders and moths known for its toughness and tensile strength.
The medical community has been aware of silk fibroin for a while. It is a common component in medical sutures and tissue engineering because of its strength and biodegradability. Yet no one had ever tried to make a dense polymer composite out of it, and that is what Wei knew she needed if she was going to create a better device for healing broken load-bearing bones.
Working with UConn associate professor Dianyun Zhang, a mechanical engineer, Wei’s lab began testing silk fibroin in various composite forms, looking for the right combination and proportion of different materials to achieve optimum strength and flexibility. The new composite certainly needed to be strong and stiff, yet not so much so that it would inhibit dense bone growth. At the same time, the composite needed to be flexible, allowing patients to retain their natural range of motion and mobility while the bone healed.
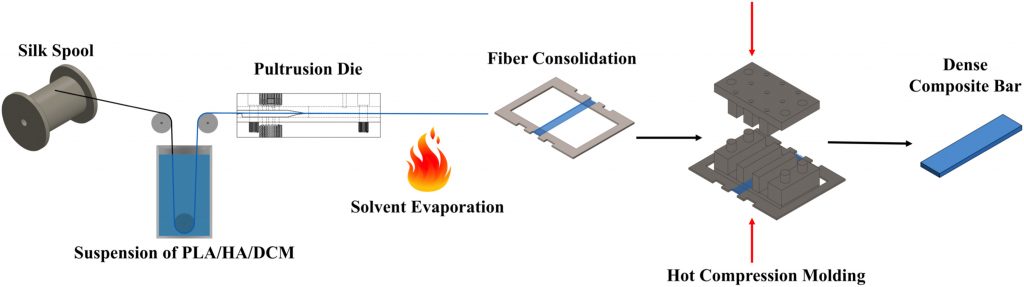
After dozens of tests, Wei and Zhang found the materials they were looking for. The new composite consists of long silk fibers and fibers of polylactic acid – a biodegradable thermoplastic derived from cornstarch and sugar cane – that are dipped in a solution in which each is coated with fine bioceramic particles made of hydroxyapatite (the calcium phosphate mineral found in teeth and bones). The coated fibers are then packed in layers on a small steel frame and pressed into a dense composite bar in a hot compression mold.
In a study recently published in the Journal of the Mechanical Behavior of Biomedical Materials, Wei reports that the high-performance biodegradable composite showed strength and flexibility characteristics that are among the highest ever recorded for similar bioresorbable materials in literature.
And they could get even better.
“Our results are really high in terms of strength and flexibility, but we feel that if we can get every component to do what we want them to do, we can get even higher,” says Wei, who also serves as the School of Engineering’s associate dean for research and graduate education.
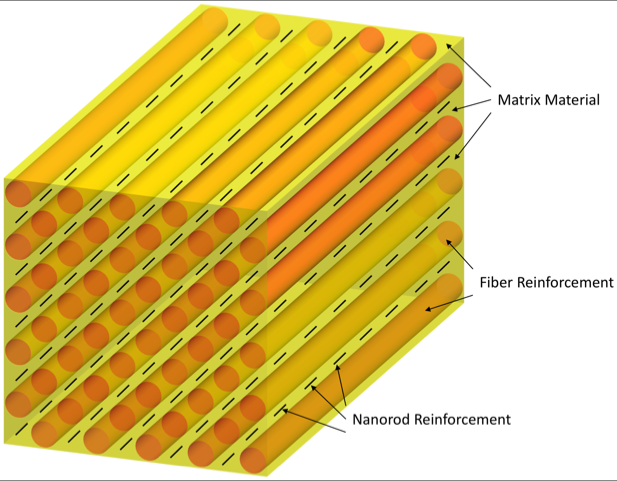
The new composite is also resilient. Large leg bones in adults and seniors can take many months to heal. The composite developed in Wei’s lab does its job and then starts to degrade after a year. No surgery is required for removal.
Joining Wei and Zhang in the research were Bryant Heimbach, a Ph.D. candidate and materials scientist in Wei’s lab; and Beril Tonyali, a UConn undergraduate pursuing a degree in materials science and engineering.
The team has already begun testing new derivatives of the composite, including those that incorporate a single crystalline form of the hydroxyapatite for greater strength and a variation of the coating mixture to maximize its mechanical properties for bones bearing more weight.
The current research was funded by a National Science Foundation grant No. 1414274 and a U.S. Department of Education GAANN Fellowship (P200A160323-17).