Hundreds of senior engineering students, their friends, faculty and advisors, representatives from sponsoring companies, and curious visitors gathered last Friday at Gampel Pavilion for Senior Design Day, the culmination of a year of collaborative, hands-on, intensive, competitive work in response to challenging engineering projects that captured the imaginations, eyes, minds and hearts of all involved.
This annual College of Engineering (CoE) rite of passage pitted student teams across all engineering disciplines to devise, design, and implement creative solutions to a spectrum of biomedical, electrical, mechanical, chemical, aerospace, civil, and computer science opportunities. The project teams, typically comprising three to five students, displayed, presented and discussed their capstone assignments, efforts and final solutions with judges earlier that morning, then demonstrated and explained their work to visitors in the afternoon. It was a deafening, raucous sea of presenting students in blue suits and business attire, and the positive energy was infectious.
“Senior Design Day is the best day of the year – it brings together students, faculty, alumni, and industrial partners to celebrate the culmination of a whole academic year of hard work,” explains Daniel Burkey, Castleman Term Professor in Engineering Innovation, and associate dean of undergraduate education and diversity. “For our seniors, it’s often the final milestone before graduation. For our first-year students, it’s an opportunity to catch a glimpse of the future. I love the big energy that Senior Design Day brings – Gampel is electric for those few hours.”
Monica Bullock, educational program administrator for engineering undergraduate programs, and assistant director of the Engineering House Learning Community, oversees logistics for Senior Design Day. Presenting skills, she explains, also are critical tools, so CoE reinforces the importance placed on communication that compliments technical capability.
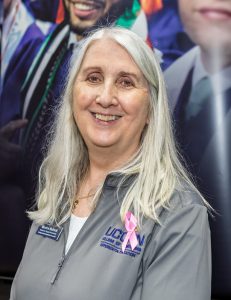
“At this point of the year,” Bullock says, “the hard work is done, so now it comes down to being able to communicate your work to the judges and the public, which can be pretty stressful. The students are worn out, it’s the final push, last days of classes, with finals looming . . . it’s a difficult time. But right to the end, we remind them, it’s the best effort that matters, no matter the challenge. And Senior Design Day epitomizes that mentality.”
The projects on display ran the gambit from manufacturing and software application solutions to biomed monitoring technologies, aerospace control designs, and even an experimental system for scaring off bears. In many cases, the student teams worked with an industry advisor as well as a CoE faculty advisor, and some of the projects reflected work that had been on the drawing board for years and resulted in viable systems and products that could be harnessed and used in manufacturing settings.
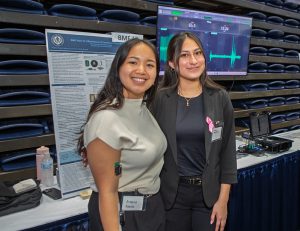
One example, from a team representing the School of Mechanical, Aerospace and Manufacturing Engineering, is the project that was built for Pursuit Aerospace, a global manufacturer of complex aircraft engine components, with several locations in New England and more than 20 locations worldwide. The design team’s creation, called the Right Sized Coil Slitter, addresses a long-term challenge Pursuit has had with excess materials that end up sitting in inventory.
It can take a year or more of lead time to procure spools of expensive metals, called coils, used to manufacture parts for aircraft engines. The company works with 76 unique coil types, used for 144 different parts. These coils often have the correct thickness, but the wrong width, and the coil width cannot be changed. Typically, Pursuit must purchase a minimum order of five coils when only one is needed. The extra rolls and remainder of the coils end up sitting in inventory.
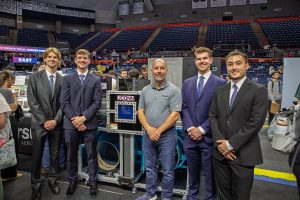
At any given time, says Allen Roy, senior director of manufacturing technology for Pursuit, and one of the project advisors, that inventory represents about $3 to $5 million in valuable metals gathering dust. He worked with the team – some of whom also have completed internships with Pursuit and have been offered employment there after they graduate – to develop a viable and affordable solution.
The CoE design team comprised Andrew Lombardi, Brendan Power, Josh Roy and Sam Walikonis. Their coil slitter utilizes a laser cutting tool to slit any coil stock material in-house to a desired width within a tight tolerance range. Pursuit technicians can then adapt the metals from the right-sized coil to a variety of parts, saving the company millions of dollars.
“We’ve sponsored other great teams, but these students are the best team I’ve worked with over the past 13 years,” Roy says. “They work together effectively and efficiently. We had a big problem that needed solving, and together they devised this brilliant solution for right-sizing inventory that will give us a competitive advantage . . . other manufacturers have the same dilemma. We’ll now duplicate the slitter and use it in other Pursuit manufacturing locations.”
Lombardi, who served as the project team leader, interned for Pursuit as a freshman and in his subsequent three years. Roy approached CoE about Lombardi and the other interns working on the inventory waste project.
“This was a collaborative solution,” Lombardi explains, “that required a lot of time and research. Having early exposure to their manufacturing environment was good training for us, as was the direction we received from our advisor, Professor Nejat Olgac, and other CoE faculty and resources. It’s been a very valuable and memorable experience.”
Lombardi says commercial coil slitters require up to 1,800 square feet and cost more than $300,000 each. Their slitter costs just under $50,000 and only requires 14 square feet, reflecting the “right-size” moniker in its name. Additionally, once these coil slitters are in place, Pursuit’s inventory areas will be significantly reduced, as they’ll be able to re-utilize almost two-thirds of their existing stock, saving the company more than $2 million.
“Working with UConn’s CoE teams is part of our workforce-development strategy,” Roy adds. “When it comes to hiring new employees, it isn’t just GPA that matters, but experience, insight and creativity. It’s a great opportunity for us, and for the students.”
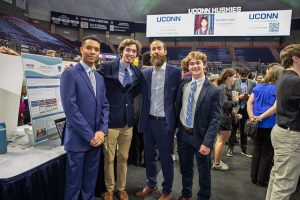
Charles Maric, director, Technical Business Development, is responsible for soliciting new project sponsorships.
“The senior design program benefits everyone involved – our students and faculty, UConn and the College of Engineering, and the many companies that sponsor engineering teams and interns,” says Maric. “Looking around this room today, you see the culmination of hundreds of hours of work that began a year ago and challenged these seniors to work collaboratively on difficult engineering assignments, with the guidance of advisors from CoE and the sponsoring organization. It’s a truly valuable, hands-on, real-world experience that helps prepare them for employment or further learning after graduation and provides potential employers with a rich pipeline of new, enthusiastic and skilled talent.”