A team of UConn College of Engineering (CoE) researchers, led by Burcu Beykal, assistant professor in CoE’s Department of Chemical and Biomolecular Engineering, have been studying methods for extracting lithium from different sources, including brines and seawater. Lithium has become an invaluable, highly sought-after resource in the fields of energy storage and sustainability, especially with the proliferation of electric vehicles and everyday electronic devices like phones and portable computers.
According to Beykal, many critical sectors—like energy, defense, and high-tech manufacturing—depend on the availability of non-substitutable resources known as critical minerals. Lithium is at the top of that list. It is the elemental backbone of modern energy storage systems, as it is the key functional material in the cathode and electrolyte of lithium-ion batteries.
Additionally, nearly one-third of all U.S. greenhouse gas emissions, primarily from carbon dioxide (CO2), come from the transportation sector, where roughly 200 billion gallons of gasoline are consumed annually, Beykal explains. And with projections for a ten-fold increase in the global electric vehicle market forecast by 2030, demand for lithium will skyrocket, as well.
“Right now, most lithium extraction happens in just a few regions globally, creating supply chain risks for the United States,” Beykal says. “My research explores how we can recover lithium more sustainably and domestically—particularly from underutilized sources like geothermal brines found here in the continental U.S. We’re asking: ‘can we design better processes to make domestic lithium recovery economically and environmentally viable?’”
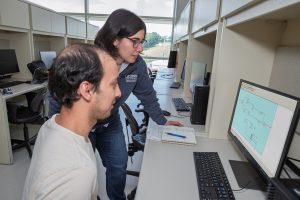
According to the United States Geological Survey’s (USGS) 2023 report, approximately 80% of the global lithium supply is allocated for battery usage, reflecting lithium’s crucial role in lithium-ion batteries as well as its significant demand across diverse industries, including light aviation alloys, glass production, catalyst manufacturing, cosmetics, and the nuclear industry.
“Without environmentally sustainable, affordable solutions, we are reaching a tipping point where demand will far outweigh lithium supply availability,” says Beykal. “Although the oceans contain a vast reserve of approximately 231.4 trillion tons of dissolved lithium, its low concentration renders lithium recovery from seawater economically nonviable. Therefore, lithium is currently only mined from hard rock ores and continental brines, such as from salt lakes, with brines accounting for 61.8%, and minerals for 25% of the total resources.”
Lithium demand outweighs supply
Based on the recent USGS report (U.S. Geological Survey, 2023), approximately 98 million metric tons of lithium resources are available globally; however, only 26 metric tons are accessible for extraction. Furthermore, with rising environmental concerns over ore and salt lake brine processing, as well as access to conventional feedstocks globally, there is a growing interest in the United States to extract lithium from unconventional sources such as geothermal brines found along the West Coast, specifically in California.
According to Beykal, geothermal brine is an emerging resource, delivering both renewable energy and essential minerals from a single operation. These hot saline solutions from the subsurface of Earth generate electricity by turning turbines when pumped to the surface. They are also rich in minerals, as the hot fluids circulating through mineral-bearing rock formations dissolve minerals and metals into the solution. High quantities of lithium, along with other valuable minerals like boron and potassium, make geothermal brines a desirable feedstock for lithium recovery. As such, the U.S. Department of Energy recognized California’s Salton Sea region as a domestic lithium resource as of November 2023.
The challenges, Beykal points out, go beyond the geographical limitations. Current extraction methods are also environmentally unsustainable, available resources aren’t easily accessible, extraction requires a significant amount of water and energy, and chemical, residual and air-borne emissions are high.
“Moreover, there is a lack of in-depth process modeling and economic and environmental evaluations of the large-scale lithium recovery process from unconventional sources,” Beykal says. “Integrating techno-economic assessment and lifecycle analysis into assessing lithium recovery processes is crucial for understanding their economic feasibility and environmental impact.”
Beykal and her team – which includes Hasan Nikkhah, Prof. Andrea Di Maria from Université de Liège, and Prof. Giuseppe Granata from KU Leuven – also are examining more efficient and environmentally friendly processes. Their work incorporates on-site recycling techniques, effectively reducing operational expenses and utilizing innovative procedures that effectively reduce carbon dioxide emissions by 50%.
Nikkhah is a graduate student working with Beykal. His research role focuses on the technical and economic aspects of lithium recovery from geothermal brine where, he says, they quickly saw significant room for improvement, particularly in integrating the lithium recovery process with carbon-capture technologies to make the process more sustainable and multipurpose.
“After developing a process model, we expanded the scope to determine how the United States can build a resilient, domestic EV supply chain,” Nikkhah explains. “We then developed mathematical models to design and optimize the supply chains, identifying where lithium extraction, battery manufacturing, and EV production plants should be located across the U.S. to meet state-by-state EV demand. The goal is to reduce total costs and decrease reliance on imports, especially given the high transportation costs associated with heavy components like batteries and EVs.”
Improving processes and reducing environmental impact
The team also proposed a novel recycling process for on-site reuse of precipitating agents, which would reduce CO2 emissions by nearly half.
“Our research seeks to develop the first end-to-end digital twin of a large-scale sustainable lithium production process from geothermal brines using chemical precipitation,” Beykal explains. “There is certainly growing attention on lithium extraction research, and we are at the forefront of this effort—building unique expertise in large-scale lithium recovery and positioning UConn and the College of Engineering as a leader in this strategically important field.”
Beykal and her team now are working to map out the broader U.S. lithium supply chain and understand how different domestic feedstocks—like geothermal brines, seawater, clays, and recycled batteries—can contribute. They also are extending their computational models to evaluate and optimize a range of extraction strategies, not just the ones they’ve studied so far.
Through this work, Nikkhah says he has gained a deeper appreciation for how complex and interconnected clean-energy systems truly are, and speaks to how valuable their work is for environmental sustainability and job creation.
“Every decision, such as where to locate a facility or how far materials must be transported, has a ripple effect on the overall efficiency, cost, and environmental impact of the supply chain,” Nikkhah stresses. “Lithium is not just a key component for clean energy but a strategic resource tied to national security and economic resilience. Through our research I learned that a domestic lithium supply chain could generate over 100,000 direct jobs in the United States. Contributing to that vision makes this work both professionally rewarding and personally meaningful.”
Two research papers, one discussing the challenges of extracting brine from unconventional sources and another examining Beykal’s work have recently been published in the Chemical Engineering Journal and Resources, Conservation and Recycling.