For weeks, the media has been warning us to shop for the holiday season now or risk being shut out of the hot-gift market. Equally troublesome is finding a new car to buy, as many dealerships have limited inventory. Even that American staple, our beloved chicken wings, have been in short supply recently.
To make sense of all this, UConn Today spoke with School of Business assistant professor Tao Lu, of the Operations and Information Management Department. Lu researches supply-chain management, transport logistics, sharing economy and socially responsible operations. We asked him about the backorders, delays and consumer-goods shortages.
What items are in most short supply? Electronics? Cars? Appliances? Computers? Toys? Chicken wings?
Everything on that list, and more, is in short supply. Home furnishings, electronics, seasonal clothing, and toys are all on the grab-them-if-you-want-them list.
The shortages that consumers are experiencing are a combination of material/component shortages, production and labor shortages, and global supply chain disruption, coupled with pandemic-induced demand. Americans are on a buying frenzy. In fact, retail sales, excluding food services, through the first six months of the year stood at $3.2 trillion, 22% higher than the same period in 2020.
Industries also face unique challenges. Cars and electronics, for instance, are hard hit by the shortage of semiconductor chips. Toys coming from Asia are experiencing lengthy shipping delays due to congestion in container lines and ports, as well as a shortage of truck drivers and warehouse spaces. Chicken wings might run out in restaurants and grocery stores because of increased consumer demand, coupled with labor shortages at farms and processing plants.
The bottleneck across the board seems to be caused by goods being stuck in transit, especially due to congestion at ports and other delivery challenges.
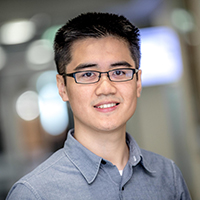
Costco recently re-enacted restrictions on bottled water, toilet paper, and cleaning supplies. Should we all be trying to stockpile?
The purchase limit at Costco is caused by a spike in consumer purchases linked to the prevalence of Delta variant cases, combined with supply-chain challenges to get items to the store.
Though the surge in demand might seem like a repeat of the panic buying that happened last year at the start of the pandemic, it is generally a more local and small-scale disruption. Supply is largely not an issue, as factories are now operating normally. Getting the merchandise to stores is taking longer, due to the supply-chain issues, and so this might cause some to wait. But the empty shelves will be short-term and temporary. So there is no need to stockpile, and stockpiling only makes things harder to find for everyone else.
What’s happening with the cargo ships? Is there a shortage of dock workers?
Cargo ships anchored near the West Coast ports, particularly in California, which handle about half of all U.S. imports, could be waiting up to four weeks to dock. Dozens of enormous cargo ships are waiting to unload up to a half million containers of merchandise. For consumers, it not only creates frustration, but also will contribute to an increase in prices. McKinsey reports that the shipping cost is now six times higher than it was in early 2019.
For example, Nike said it is taking 80 days to move a sneaker from Asia to the United States, double the time it did in the past. The company blames it on a combination of port congestion, container shortages, rail congestion, and a labor shortage.
A successful supply-chain process requires that all aspects of the process are working efficiently and collectively. Once the cargo ships have docked, the system is encountering a shortage of dock workers, who must follow social distancing and quarantine practices like everyone else. There has also been a shipping container shortage, often blamed on a logistics shortcoming, with containers being stored in the wrong places. Even if there are enough dock workers to unload the containers, it won’t help much if there are not enough truck drivers to pull away the containers, or if there is not enough warehouse space to stock the goods they unload. Shipping is a complex system. If one link in the supply chain faces a severe problem, it can knock the whole system out of whack.
When the pandemic started, shipping companies cut back on capacities as they were afraid of the decline in future demand. As the economy worldwide is coming back to normal, shipping demand has increased but shipping capacity needs time to recover.
Is it surprising to have this problem at this late stage of the pandemic? Do you expect shortages to carry over in 2022 or is this just a passing anomaly?
It is not surprising. Building up capacity takes more time than demand increases. The supply will eventually catch up with demand. Hopefully, by coordinating various parties in the supply chain, we can soon have supply match demand again.
Retailers are looking at Summer 2022 as a full supply-chain recovery. So don’t give up on getting your favorite jeans or that new computer. It might just take longer than you’d like, but it will get here eventually.