A team of UConn chemists led by professors Steven Suib and James Rusling has developed a new material that could make hydrogen capture more commercially viable, and provide a key element for a new generation of cheaper, light-weight hydrogen fuel cells.
The new metal-free catalyst uses carbon graphene nanotubes infused with sulfur.
Hydrogen is the most abundant element in the universe and a promising source for clean energy. But producing high-grade hydrogen is an expensive and energy-consuming process. Often, the energy spent extracting hydrogen is worth more than the hydrogen gas it produces. Finding a cheaper and more efficient way of capturing hydrogen would go a long way toward the creation of a sustainable hydrogen economy, and would help reduce the world’s reliance on fossil fuels.
“We’ve made a material that looks pretty good,” says Suib, Board of Trustees Distinguished Professor of Chemistry and director of UConn’s Institute of Materials Science. “Our results show that this material is more than competitive with the state-of-the-art materials quoted in literature, and exceptionally good for the reactions we need.”
Current hydrogen production uses intense heat to separate hydrogen from hydrocarbons found in crude oil. But the resulting hydrogen isn’t very pure, and byproducts must be scrubbed out.
An alternate process, capturing hydrogen in water, is cleaner and more sustainable, but it too has limitations. Electrocatalysts involved in this process are usually made of rare earth metals like platinum and iridium. But they are very expensive, making the commercialization of pure hydrogen fuels difficult.
Finding a non-metal catalyst that has all of the electrochemical properties of the rare earth metals but can be made at a much reduced cost and still remain stable has been a goal of scientists for years.
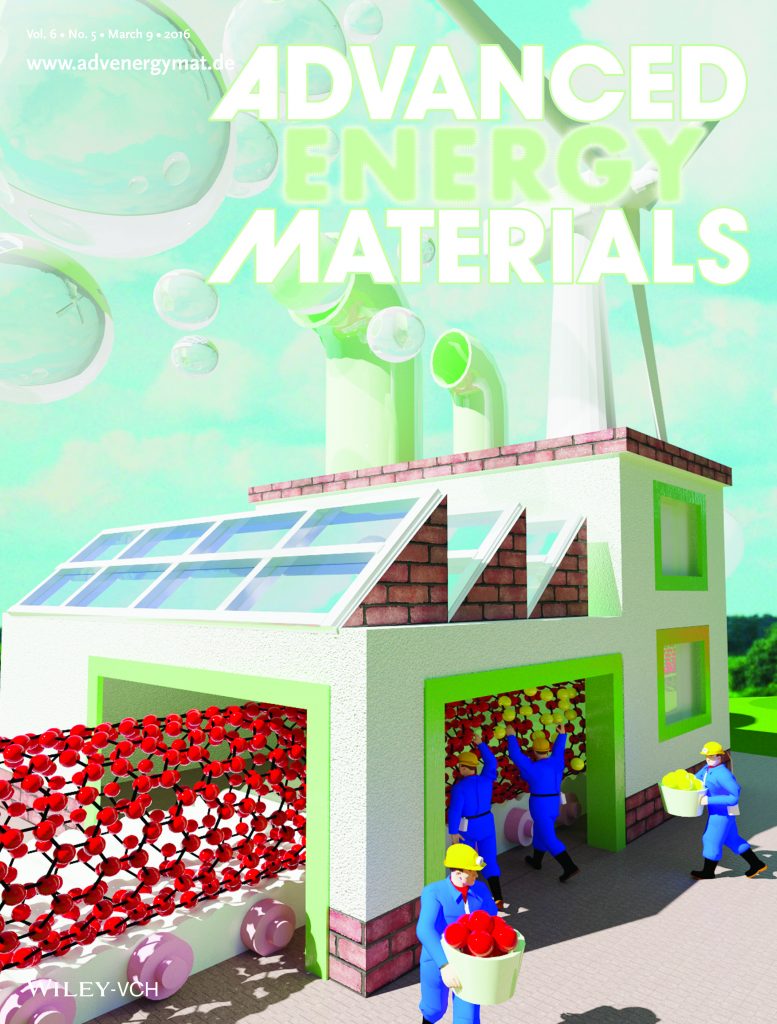
Suib and Rusling, an expert in electrochemistry, knew that sulfur-infused carbon graphene nanotubes were a potentially efficient non-metal catalyst for an oxygen reduction reaction. An oxygen reduction reaction, or ORR, happens when oxygen and hydrogen molecules are converted to water. The reaction is a key component of hydrogen-based fuel cells. Hydrogen gas used to power the cells passes through a catalyst, currently a corrosive-resistant metal like platinum, causing an oxygen reduction electrochemical reaction that creates energy and – as a byproduct – water.
But reversing that process – starting with water and extracting pure hydrogen from it, a procedure known as an oxygen evolution reaction – is much more of a challenge electrochemically. Suib and Rusling, working with a team of graduate students led by Ph.D. candidates Abdelhamid El-Sawy and Islam Mosa, decided to give it a shot.
The key, Suib says, was manipulating the sulfur and carbon atoms to create stable bonds and structures within the nanotubes, while also maintaining or improving the tubes’ electrochemical potential so that it mirrored those found in the rare metals.
“If you are going to make a hydrogen economy, you need to have new materials that do the same thing as the extremely expensive rare earth metals,” says Suib. “But how do you get something that is cheap, durable, and stable enough to be scaled up to industry levels? That was our challenge.”
The process developed in Suib’s and Rusling’s labs uses a dual doping procedure involving sulfur and benzyl disulfide treated at high heat. The researchers had to carefully add heteroatoms of sulfur at extremely low levels to strike the delicate balance needed to maintain usability and stability. Add too much sulfur and the sample would be unstable; not enough and it would be ineffective.
Suib says the procedure for isolating hydrogen in water, in a very general way, is similar to trying to separate flour and sand after they’ve been mixed together thoroughly.
In the end, he says, the sulfur-doped nanotubes used much less energy in the chemical reaction process than other known processes, and were much more active and efficient catalysts than other known products.
Most importantly, he points out, the sulfur-infused nanotubes are efficient for both separating hydrogen from water and reducing oxygen into water. Materials with those dual properties are rare, he notes.
“I was surprised, in the end, that it worked so well,” Suib says, with a grin. “We thought it might work, but we didn’t think it would work so well.”
Powerful transmission electron microscopes and scanning electron microscopes in UConn’s Bioscience Electron Microscopy Lab, Institute of Materials Science, and new FEI Center for Advanced Microscopy and Materials Analysis were instrumental in helping researchers test and characterize the new material as it developed in the lab, Suib says.
The research was funded by the U.S. Department of Energy’s Office of Basic Energy Sciences. The full report is featured in the March 2016 issue of Advanced Energy Materials: A.M. El-Sawy et al., “Oxygen Reactions: Controlling the Active Sites of Sulfur-Doped Carbon Nanotube–Graphene Nanolobes for Highly Efficient Oxygen Evolution and Reduction Catalysis,” Advanced Energy Materials, 2016, Vol. 6, no. 5. Artwork associated with the research was featured on the Journal’s cover, and is reproduced on this page with permission from Wiley-VCH Verlag GmbH & Co. KGaA.