Eddy Ramos is deeply interested in design and manufacturing.
Kaley Luk is an eco-captain with a passion for sustainability.
Patrick Miconi enjoys working with his hands.
And Leila Awad hopes to one day work in project management.
These four UConn seniors, all working toward graduating from the UConn School of Engineering this May, didn’t really know each other when they were chosen to work together as a team on their Senior Design project in the Fall 2022 semester.
But the task they were given to complete for their undergraduate capstone was the one that all of them – and most of the rest of their Mechanical Engineering classmates – really wanted: the ramp project.
“It was number one for everyone,” says Luk.
“This was actually the top project that our Senior Design class wanted,” agrees Awad.
Senior Design is a hallmark of the School of Engineering’s undergraduate programs. The two-semester course, a graduation requirement, engages students as teams that work to solve real-life engineering problems for industry and private sponsors.
Students learn and experience the importance of schedules, communication, budget constraints, goal setting, deliverables, customer expectations, and solving problems – like the problem of how to build a better, affordable, sustainable, and modular accessibility ramp.
The Project
Bill Wiggin knows a lot about solving problems. He’s done some interesting things in his life: advising Connecticut politicians and pastors, starting and selling businesses, identifying problems and then finding solutions.
“I’ve never been traditional,” he says. “I’ve always been unique in what I’ve done, for better or worse.”
A few years ago, after Wiggin was diagnosed with cancer, someone close to him became disabled. For both of their sakes, Wiggin began thinking ahead to their possible future mobility needs and started making arrangements for aid and in-home accessibility.
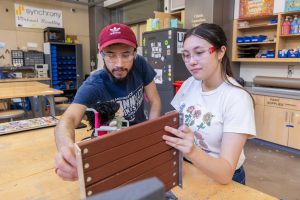
But even with a lifetime of connections, and a familiarity with the workings of state government far greater than most average Connecticut residents, one persistent problem peeved him: how to get a ramp.
“The overriding thought about health care in Connecticut is to keep people in their homes as long as possible,” Wiggin says. “Well, it seems to me the first consideration should be, can they get in their homes? They have all these processes in the state of Connecticut – clerical processes, applications – clear paths to all sorts of decisions of every kind, right down to the railings for the bathtub and all these things that are clearly marked on applications and you can easily get. There’s no clear path to getting a ramp.”
A quick internet search offers dozens of private companies selling different styles of wheelchair and accessibility ramps, but actually getting one isn’t always so simple.
“I called up to say, I need a railing in my bathroom. You know what the response was? ‘OK. Fill out this, sign that. Whatever it was. You got it,’” explains Wiggin. “Whenever I called up on a ramp, I’d say there’s a problem getting ramps. What I heard was, ‘yeah, ain’t there?’”
Some ramps on the market are portable, and some are meant to be installed in a permanent, outdoor location, like the entryway of a house. Most permanent ramps are made of aluminum, which are complicated to construct, or wood, which will degrade in Connecticut’s climate and require repairs over time.
Permanent ramps can cost thousands of dollars, and most are complex to build, requiring professional installation on top of their purchase price. For people dealing with high medical bills, limited mobility, or a fixed income, getting a ramp installed at their home can be a unique challenge.
“If you go to Connecticut’s website, and you look at how to afford a ramp, it’ll send you to several nonprofits,” says Edith Barrett, a professor emeritus with UConn’s School of Public Policy. “I’ve talked to several of them, and they’ll give you low-interest loans, but they don’t give out ramps for free. Only if you’re a veteran, and Medicare will pay some, but they’re not going to pay a lot. For people who are on the cusp of not qualifying, if they have to put up a thousand dollars for a ramp, that’s a lot of money.”
Barrett met Wiggin in 2021 when he audited a class she was teaching on social policy at UConn Hartford. They spoke about his ramp dilemma and how he was at that time considering approaching the Connecticut General Assembly to try to create new policy that would offer greater options for people trying to get accessibility ramps.
“That’s how it all started, and that’s how I got involved,” Barrett says. “Let’s see if we can’t go to the legislature and get policy created where the state legislature will help lower-income people afford ramps.”
But what started as just a conversation about policy has taken on a life of its own since those early conversations.
“We got to talking about affordability of ramps, in general,” she says, “and we got to brainstorming. I said, you know those playgrounds for children that are made of high-density plastics? I wonder if we could make a wheelchair ramp out of high-density plastics. Then it would be recyclable, it would be recycled, it would be sustainable, and it could be affordable. And Bill said, well, how about if we do it like Legos, where you can just put it together? And that is the brainstorm that we took to the students at UConn.”
The Deliverable
Barrett and Wiggin brought their recycled plastic ramp idea to the faculty leaders of Mechanical Engineering’s Senior Design in summer 2022. The project was accepted into the program – it’s supported by the College of Liberal Arts and Sciences, through Barrett’s faculty development fund – and the student team was assigned and got to work in the fall.
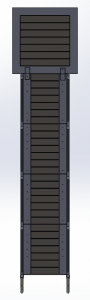
“Our objective is to design and create a prototype accessibility ramp that is affordable and modular, as well as having an emphasis on construction through recycled materials,” Ramos explains.
The design also had to adhere to the ramp requirements specified in the federal Americans with Disabilities Act, or ADA, which defines appropriate slope, rise, width, length, edge, handrail, and landing requirements for ramps.
They spent the fall semester researching existing ramps and beginning their initial, modular design, with each member of the team contributing and collaborating on the design itself, but also leaning into their own personal strengths.
Awad has helped organize meetings and keep the team on track while also contributing to design and working on a finite element analysis, or FEA, for the project, which is used to analyze how a design reacts under real-world conditions when dealing with issues like heating and cooling, vibration, structural support, and water flow.
“Everyone contributes their own expertise to the group,” she says.
Luk, who cares deeply about sustainability, focused on how their project could be better for the environment than other ramp options. She also is interested in design and helped contribute to the final concept for the ramp’s handrails, and she became the team’s knowledgeable go-to on compliance with ADA requirements.
“I bounce around where I’m needed,” Luk says. “I do keep track of the ADA. We almost had a big mistake with the landing. I noticed that the size seemed kind of off, and it turns out that it was almost going to be too small. Luckily, that’s something we caught.”
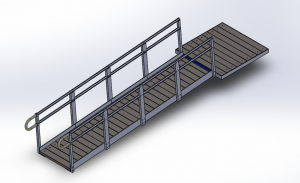
While both Miconi and Ramos initially both worked on modeling the team’s design concept, Ramos took the lead as the project progressed from initial thoughts to really optimizing their concept.
“It is a lot more difficult to do very basic things than people might imagine,” Ramos says. “At least at a first glance, the shapes of our design seem very simple. They’re not incredibly complex. We’re not building an airplane engine here, so you don’t have a bunch of different splines and complex geometries. But it’s still difficult to construct, and then to assemble, and then to optimize from that point forward, and then remodel, rebuild, and reassemble.”
Miconi, who has experience with metal work and construction, took on the primary role in constructing the team’s physical third-scale prototype. The project is also deeply personal for Miconi, who lived with disability as a child.
“I went from wheelchair to walker to crutches to leg braces,” he says, “and while I was disabled and in my wheelchair, I felt like I couldn’t be as independent as I wanted to be because I needed so much help. I was so fortunate that my parents were always able to support me when I needed physical assistance, but not everyone has that, and ramps are expensive.
“So, it’s a very personal reason why I want these to be cheaper. Even if it’s a temporary thing for people, like it was for me, fortunately, that it’s something that people can afford for quality-of-life assurance.”
In the fall, the team also began researching and sourcing material options, which proved challenging as supply-chain issues in late 2022 made ordering the recycled high-density polyethylene, or HDPE, lumber they hoped to use more difficult. They eventually settled on using a sustainable HDPE fiberglass lumber made from recycled milk jugs and laundry detergent containers as their primary material.
Their final design relies on an aluminum angle that acts as a frame to support the beams and handrail sections, which are made to be interchangeable and optimized to use simple bolts to connect the pieces together. The universality of the pieces not only makes manufacturing easier, the students explain, it also helps ensure that the ramp can be customized to fit each person’s home, doorway, and yard.
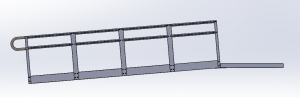
“That’s part of the modularity aspect,” Ramos says. “We want you to be able to say, well, I can’t go right, because the configuration of my house doesn’t allow for that. I need to navigate some kind of obstacle – maybe I have a tree in the way – and I want to be able to go left, or I need to go straight, in this scenario. You can do that. You would just basically start connecting your other run sections in whatever configuration you may need, and you do it piece-by-piece, connecting each section to another section.”
“The final way I would propose to the sponsors on how they should actually sell our accessibility ramp design is they would sell it by section, versus a whole accessibility ramp kit,” adds Awad, “because each home is very unique.”
Additionally, each individual piece of the ramp weighs less than 30 pounds – another important requirement of the design.
“A main goal with our assembly is that, maybe they can’t put it together themself, but they can hire the high school kid next door,” says Miconi. “It’s Ikea-level design, so it can be put together fairly easily.”
The Future
The engineering students will present their project alongside other Senior Design teams on April 28 at the School of Engineering’s annual Demonstration Day. While they’ve been meeting with Barrett and Wiggin about their progress every few weeks throughout these two semesters, Demo Day will mark the first time the project sponsors get to see the actual prototype in-person.
“I think they’ve really been taking to heart all the things that we’ve been saying, that we want it to be something that you or I could put together – anyone who could put together an Ikea desk can put together this ramp,” says Barrett. “We want the pieces to not be very heavy, so they have paid attention to that. We want as much recycled material as possible, so they’ve been paying attention to that.”
For Wiggin, working with the students has been “more than wonderful.”
“It’s energizing,” he says. “It’s life-giving. It’s like getting a jumpstart. Their desire to do good, to change the world for the better, and for me to be a part of affording them that opportunity, life doesn’t get any better than that. It really doesn’t.”
For Wiggin and Barrett, Demo Day also marks another step in the process toward making ramps more accessible and affordable for the Connecticut residents who need them. They’re still planning to take their initiative to the state legislature, and they’re launching a 501(c)(3) nonprofit organization, called The Earth Friendly Project, through which they hope to leverage public-private partnerships to help get ramps to those who need them, but also to help bring the UConn student-designed ramp – which they’re calling Eco Entry – into reality.
“We never wanted this to be entrepreneurial,” Barrett says. “That’s never what we intended to do. Our intention was always to make ramps accessible to lower-income people,” something that makes sense from a public policy standpoint.
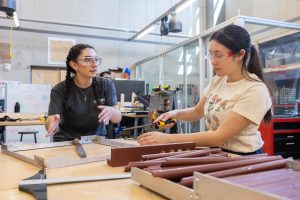
“It’s in the state’s best interest to help people stay in their homes,” she says. “It’s most affordable for people to be able to stay in their home. Not have to go into nursing care. Not have to go into assisted living care. The longer they can stay in their homes, the less expensive it is on everybody, and the better quality of life it is for the individuals.”
“We want to be completely different,” says Wiggin. “We’ve got to be different in order to bring this home. I want to re-conceptualize the distribution process – I want to re-conceptualize on every level. I want to completely re-conceptualize the last mile, because I don’t think there is one on this. I want to build it, and I want to re-conceptualize the way a ramp is designed.”
While the four members of the student team don’t see themselves launching a company or starting to manufacture their ramp design on their own, they hope their work will be a jumping off point for a future Senior Design team to optimize even further – or for Wiggin and Barrett to take their existing design to the next level.
“I know a big problem for people in the disabled community is independence,” says Miconi. “A lot of times, they feel like because of their disability, their independence has, to some extent, been taken away from them. We want this ramp to ensure that, at least for some aspects of their life that are impacted by their disability, they still have that independence.”
But they all agreed that the team experience – from working together to problem solving to integrating sustainability in their modeling – is one that’s helped to prepare them for the next stage in their lives, as they look forward to graduation and entering the world as the next generation of mechanical engineers.
“One of the things that I’ve gained from Senior Design is the ability to bounce back in the sense that, when I come across a problem, I’m able to now think in a way that this problem isn’t the end-all,” says Awad. “There can be solutions. It’s already giving us a head start on how to think in an engineering mindset.”
Doors will open for the School of Engineering’s 2023 Senior Design Demonstration Day at 1:00 p.m. on Friday, April 28, at Gampel Pavilion in Storrs. For more information, about Demo Day and about Senior Design at UConn, visit seniordesignday.engr.uconn.edu.
For more information about The Earth Friendly Project and it’s Eco Entry ramps, contact Bill Wiggin at billwiggin@hotmail.com.