Despite a growing population on the Storrs campus and increasing concerns about water conservation, the steps that UConn is taking to be more sustainable are paying off.
In 2013, UConn’s Reclaimed Water Facility (RWF) began providing hundreds of thousands of gallons of reclaimed water to campus every day, meaning less potable water is used to keep the campus running, for things like heating and cooling to flushing toilets in some buildings. This state-of-the-art facility serves as a case study for other institutions, and has been an integral part of UConn’s water usage reduction strategy.
UConn maintains and operates a wastewater treatment plant, or Water Resource Recovery Facility (WRRF), which takes in and treats all the wastewater generated on campus. The WRRF is designed to treat up to three million gallons of wastewater per day. While most of the treated water is discharged safely back to the environment, a portion of the water is “reclaimed” by the RWF, where additional treatment takes place so the water can be used for non-potable purposes on campus.
“By reclaiming treated wastewater for use on campus, we can significantly reduce the amount of potable water needed to be drawn from drinking water sources for non-potable uses,” says Jacob Fortin ‘20 (ENG), now a Project Engineer at Woodard & Curran, a consulting firm working with UConn to operate the RWF. Fortin started interning at the facility as a sophomore undergraduate, and he now works full-time for the company. He often leads tours of the RWF and explains how it all works.
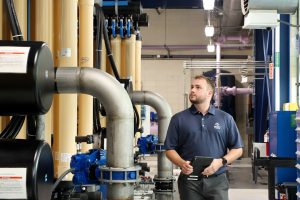
“The largest users on campus are the Central Utilities Plant (CUP) and the Supplemental Utilities Plant (SUP), which use reclaimed water in their boilers and cooling towers for electrical and steam generation. Reclaimed water is also used for cooling at the Innovation Partnership Building (IPB), in the toilets of several buildings around campus, and can even be used as jetting water for sewer cleaning. We are also looking ahead at future uses for reclaimed water on campus, most recently pursuing permits for irrigation,” says Fortin.
The process from wastewater to reclaimed water is thorough. The influent water for the RWF comes from the WRRF’s chlorine contact tanks, where the final wastewater treatment processes of chlorination and dechlorination are performed. Fortin explains that while it is necessary to remove residual chlorine in the effluent water discharged to the environment, the RWF actually takes in the wastewater prior to dechlorination. This allows the residual chlorine to continue working, and can save on operation and maintenance costs.
“The plant was designed to process up to a million gallons per day, but the current average demand isn’t that high, so we have the capacity for future production,” says Fortin. The RWF currently produces anywhere from 250,000 to 450,000 gallons of reclaimed water per day.
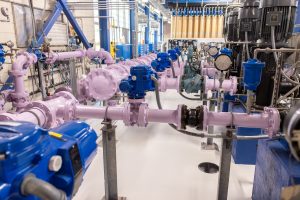
Inside, the RWF is bright and colorful, with surfaces and pipes painted to address specific safety concerns.
“All of our pipes are labeled or colored based on the contents inside the pipe. Green pipes are influent wastewater, purple is reclaimed water, and chemical pipes have yellow and orange labels. The floors are painted white, which keeps everything brighter, and we have opaque walls, which allow natural light in,” says Fortin. “Raised surfaces are painted blue so they can be seen against the white floor, potentially wet areas are painted gray, and any potential trip hazards are pained yellow.”
Wastewater from the chlorine contact tanks flows by gravity to the RWF, where vertical turbine pumps send up to 480 gallons per minute (gpm) through the treatment processes. Nearly all the pumps at the facility use Variable Frequency Drives (VFDs) to control the volume of water flowing through the system. Fortin explains that VFDs allow the facility to adjust the speed of the pumps based on demand, which means the plant won’t waste energy running pumps at higher speeds than necessary.
The first stage of the reclaimed water treatment process uses an auto strainer which filters out all solids larger than half a millimeter. “Anything that gets filtered out is flushed down the drain during cleaning, and anything that goes down the drain is pumped back up to the WRRF for retreatment in a closed-loop system,” says Fortin.
The next step in the process is running the water through tall, cylindrical microfiltration units. Fortin explains that the microfilters are composed of tiny fiber-like straws arranged within the columns, where anything larger than 0.1 micron gets filtered out. After microfiltration, the next step is a UV sterilization process that happens in large, horizontal tanks and kills or sterilizes 99.99% of the targeted organisms.
“Sterilization either kills or sterilizes the organisms remaining in the water because the dose of UV light affects their DNA. A lot of those organisms may not be dangerous in small numbers, but through sterilization, they are at a minimum prevented from reproducing in the storage tank,” Fortin says.
These three steps are the bulk of the processes, Fortin explains, but the RWF can add chlorine to the facility’s influent water, discharge, or storage tank to provide supplemental chlorine disinfection if needed.
Three in-line monitoring stations are continuously measuring and recording real-time water quality data before the treatment process, after the treatment process, and as the water is discharged from the facility. Additionally, the RWF has an in-house laboratory and performs daily testing to verify water quality is sufficient.
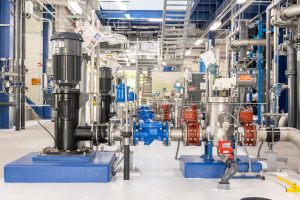
At this point, the reclaimed water is sent out to the million-gallon storage tank. The tank level is usually kept about half full, which is generally enough to meet the daily demand, but it also gives the plant and its operators some flexibility, says Fortin. The tank level can be adjusted by processing more or less water through the RWF, which is generally dependent on the daily demand, maintenance planning, or in preparation for increased or decreased demand, depending on the volume of users on campus. Fortin adds that it is also easier to make adjustments to half a million gallons of water than it is to adjust a million gallons.
From the storage tank, the water flows to campus with the help of three pumps, where it is delivered to the CUP, the Engineering and Science Building, the Gant Complex, the Innovation Partnership Building, Science 1, and the Supplemental Utility Plant.
The RWF was built with sustainability in mind, beyond saving water. There is an eight-kilowatt solar array on the roof to help provide power, and all the facility’s lights are LEDs. It was also designed to harvest rainwater with a gravel roof that drains into a separate pump station that feeds the rainwater into the facility influent. Fortin explains rainwater has a low conductivity, one of the key water quality parameters continuously monitored at the facility, compared to the wastewater undergoing treatment. Generally, when the conductivity increases in the storage tank, a small quantity of potable water is blended into the tank; rainwater, however, can be used in place of blending water which is a sustainable method of conserving potable water for use on campus.
Reclaiming water reduces the university’s environmental footprint while also conserving drinking water sources for future uses. — Jacob Fortin ‘20 (ENG)
“Since the Reclaimed Water Facility came online, it has reclaimed hundreds of millions of gallons of wastewater for reuse on campus that would otherwise have been drawn from the watershed sources. Reclaiming water reduces the university’s environmental footprint while also conserving drinking water sources for future uses. And as UConn continues to grow and innovate, we are always looking for new ways to incorporate reclaimed water on campus and teach the community about the benefits of reclaimed water to promote a more sustainable university,” Fortin says
So, if you see purple pipes, remember they are part of a sustainable process that turns wastewater into a vital resource.