If there’s one thing Christopher Sancomb freely admits, it’s that he likes things like foamed aluminum, pieces of copper, chunks of iron, and sticks of ebony.
“I’ve always been a materials person,” says Sancomb, an assistant professor of industrial design in the Department of Art and Art History. “It’s always been a big part of my work.”
For 15 years before coming to UConn in 2019, Sancomb designed museum exhibitions for children, a job that required him to carefully consider each material he planned to use: Would it do what he wanted it to do? Is it environmentally friendly? How hard is it to obtain? Can it be ethically sourced?
“That began my collection and fostered a deeper interest into all the things that go along with the stuff we use in the world,” he says.
Industrial designers and engineers – really, anyone who builds something from scratch – must think about things like this when working on projects, he says, and until now UConn students studying for these professions had no place to learn about the infinite number of materials available in the world.
Sancomb has changed that.
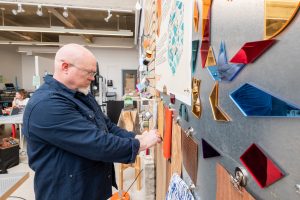
UConn’s Materials Library, of which he is founder, has been a project five years in the making, stalled by the pandemic but now finishing its first year as a resource for students and faculty.
In the rear of the Art Design Center – that’s Room 108 in the Art Building – the library houses a collection of raw, manufactured, and reclaimed materials from all over the world that go into the built environment around us, he explains.
“We want to use this as a hands-on learning space, so you can see the thing, touch the thing, measure it, mark it, uncover where it comes from, learn more about it as a way to understand what we use in the world, what we put into the world as designers,” he says.
It’s a place where people can feel the weight of a brick of mycelium, the gentleness of a tuft of alpaca wool, the grooves of a crocodile pattern on a piece of bioleather, and the sturdiness of recycled plastic turned into a 1.5-inch-thick felt-like board.
It’s a place to refine ideas, develop new ones, and spark creativity.
“Let’s say you came in and were thinking of using an existing plastic that had certain qualities – maybe it needs a high breaking strength and high UV sensitivity. Maybe it needs to be washed and sanitized. Traditional plastics from the petrochemical world might work, but the library would show you there are alternative biomaterials that are just as well-suited and they’re less toxic,” he says.
Assessing Alternatives Through Hands-on Research
Samantha Wilkins ’25 (ENG) freely admits that she loves everything about airplanes, from the ailerons to the yaw string. There’s just something about them, she says.
As one of five interns at the Materials Library this academic year – each with their own research project in addition to helping Sancomb establish the library – she’s been thinking about sustainable aviation.
What alternative textiles can be used as seat covers and cushions? What plant-based products can form the cabin’s airframe?
“We have a bunch of different materials in here that I didn’t even know existed,” she says of the library.
Take hemp, for example.
“I was doing a lot of research and found an aircraft designer who made a completely sustainable, flyable aircraft out of hemp because it comes in all different forms. He made the entire fuselage structure out of it. This is just the textile version,” Wilkins, a multidisciplinary engineering major who’s concentrating in industrial design, says as she holds a fabric hemp sample in her hand.
“I’ve been researching a lot about hemp, jute, flax, things like that and the different forms they can take,” she says. “It really intrigues me that you can have so many different forms from one single material and it can serve so many different uses. I love that.”
Pamela Mackingue ’26 (SFA) says that after working as an intern this year, hemp also has become one of her new favorite things.
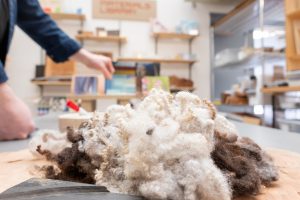
The double major in digital media and design and art with a concentration in industrial design says she’s focused her research on the fashion industry and finding materials that are more sustainable than many other products used today.
She’s growing her own leather – out of kombucha – fermenting black tea to create a biofilm that can be dried out to resemble the texture of animal leather, conditioned to restore some of its natural oils, and dyed any color in the rainbow. What she freely admits is that it’s not her own novel idea – it’s a process she came across while researching sustainable leather alternatives.
“As a designer, you have to think about the product you’re using, why you’re using it, what’s the purpose of it, how does it help your design,” she says. “It’s important information to know and getting that hands-on experience in the Materials Library is equally important.”
In addition to their research projects, Sancomb says the interns are helping him with the day-to-day work of the library – that is, cataloging each item and deciding what information is important for someone to know, then putting that information into a database, which eventually will go online.
Nonetheless, Wilkins says, “You can look at a database or inventory, but you don’t really know what you’re looking for until you get in here. The hands-on element is super important. A database can help you grasp the basics, then you can come in here to narrow down the possibilities and interact with the material you settled on.”
Personal Belongings, Donated Items, Purchased and Procured Objects
Sancomb opens the lid of an old cardboard box labeled “Constantine’s Rare Collection of the World’s Fine Woods” and carefully lifts out rectangle samples of cabinet wood veneer. They’re about 50 years old, he says, and were a donation from a friend.
Each of the 50 samples no doubt has a story, he says. Some of the wood might have been over forested and no longer is available. Some might have been the root of a humanitarian conflict. Some might be lost to forest fires and labor disputes.
“I find it really interesting the stories that can be told just from this collection and what might be in here that’s just gone,” he says.
With hundreds of items in the library, Sancomb says the collection includes some of his personal belongings like a chunk of marble with machined, cut, and polished faces brought back after a research trip to Italy, along with donated items like a bag of wool from UConn’s farm.
Other items have been purchased or procured without a cost other than a written request. No hazardous materials are part of the collection, and nothing is of significant monetary value – important things, Sancomb says, to keep the library freely open for all.
“My students are required at different times to think about the library and work with it, but we want students from other disciplines to know they can come here and access the materials,” he says.
UConn Bound in April drew dozens of prospective students and their families, and a steady stream of people came through during an open house the month prior, everyone wanting to see the library, which surprisingly isn’t something all schools have.
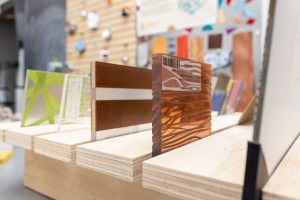
The Rhode Island School of Design has a materials library, and so does the Harvard Graduate School of Design and the University of Texas at Austin, but not every school with an industrial design program boasts such a research space, Sancomb says.
Over the next decade, he says he hopes UConn’s library can outgrow its current home and move into a larger, more permanent location, maybe joining with another library on campus to bring its catalog to the UConn community.
Its hundreds of items could become thousands, with Connecticut industries and Connecticut products figuring prominently, he envisions. A larger budget would allow for more acquisitions, although donations likely will always be accepted.
“We recently got a large donation of wood and veneer,” Sancomb says, “so we’re working to catalog that collection and make it available to students through an application process. This way, if someone got an IDEA grant and needed to build some furniture, for instance, they might come to us with a proposal, and we would help supply them.”
Sancomb reaches across a table and hands off a small block of what looks like compressed soda can flip-tops.
Imagine that someone dipped a straw into a vat of molten aluminum and blew bubbles, he says. This is the solidified result, light airy panels of foamed aluminum that are sturdy enough for some structural applications, like for insulation or exterior cladding.
“They’re sound-dampening. They have a high fire retardancy because they’re made of metal, and they’re recyclable,” Sancomb says. “It’s a visually stunning material because you look at it and ask, ‘Is this what I think it is?’ And it is.”
Donations of raw, manufactured, and reclaimed items can be made to the Materials Library by emailing Sancomb at christopher.sancomb@uconn.edu. Check out @uconnindustrialdesign on Instagram for its Material Monday campaign, featuring materials that might not be in the library but have interesting backstories.